
국부 감육과 균열이 발생한 TP316 스테인리스강 배관의 파괴거동에 관한 실험적 연구
초록
원자력 배관 시스템은 엄격한 설계기준에 따라 제작 되었음에도 불구하고, 장기 사용에 따라 발생하는 감육 및 균열에 의한 파손사례가 보고되고 있다. 이에 본 연구에서는 스테인리스강 배관 시험체의 단조하중 및 반복하중 재하실험을 실시하여 국부 감육과 균열의 손상유무 및 0%, 35%, 75%의 손상정도가 배관의 파괴거동에 미치는 영향을 실험적으로 검토하였다. 본 실험에서는 실제 원자력 발전소에서 사용되고 있는 직경 3인치 TP316 스테인리스강 엘보우와 직관 배관을 대상으로 하여, 인위적으로 곡관부와 용접부에 0%, 35%, 75%의 국부적인 감육과 균열을 도입하고 20MPa의 내압을 가한 후 재하실험을 실시하였다. 그 결과, 국부 감육 및 균열의 손상정도가 파괴모드, 최대하중, 반복회수 및 에너지흡수율에 미치는 영향을 정량적으로 평가하였다. 그리고 휨 모멘트를 이용하여 ASME의 결함 허용기준을 평가하였다.
Abstract
Although nuclear power plant piping system is designed conforming to design specifications, the piping systems are deteriorated with increase in service life. In this study, monotonic and cyclic loading tests were carried out on TP316 stainless steel pipe specimens, and the effect of local wall thinning and cracking on failure behavior was investigated. In the tests, 0%, 35% and 75% wall thinning and cracking of initial thickness were artificially introduced to inside elbow and straight pipe specimens, and internal pressures of 20MPa were applied to simulate real operation condition. From the test results, the effect of local wall thinning and cracking on failure mode, ultimate load, number of cycle and strain energy was presented, and maximum bending moment was compared with allowable bending moment calculated by ASME code.
키워드:
스테인리스강, 엘보우, 직관, 단조하중, 반복하중, 감육, 균열, 파괴거동Keywords:
stainless steel, elbow, straight pipe, monotonic load, cyclic load, wall thinning, cracking, failure behavior1. 서 론
최근 환경문제 및 에너지 절약에 대한 관심이 증가하고 있지만, 에너지 소비량 또한 증가하고 있는 경향에 있다. 그러므로 석유 대체 에너지로서 원자력 발전이 주목되어 왔으며, 앞으로도 한층 더 그 중요성이 증가할 것으로 예상된다.
1986년 4월에 발생한 체르노빌 원자력발전소와 2011년 3월 후쿠시마 원자력발전소의 사고와 같이, 원자력 발전소에서 사 고가 발생하는 경우에 그 피해는 막대하다. 따라서 원자력발전소에는 고도의 안전성과 신뢰성이 요구된다.
원자력발전소의 냉각 및 발전시스템은 복잡한 배관으로 구성되어 있다. 그 중 냉각시스템은 운전 중에 발생하는 고온 및 고압 유체의 이송을 주로 담당하고 있으며, 다양한 하중과 환경에 노출되어 다양한 형태의 결함 발생 가능성을 가지고 있다[1]. 그리고 이와 같은 배관계에 손상이 발생한 경우에는 원자력 발전소의 전체 시스템에 악 영향을 미쳐 막대한 피해를 유발시킬 우려가 있다.
배관계의 대표적인 손상요인은 응력부식균열에 의한 균열과 에로젼/코로젼(Erosion/Corrosion)에 의한 감육을 들 수 있다[2],[3],[4],[5],[6]. 배관의 감육에 대해서는 실험적 및 해석적 검토를 통한 다수의 연구가 수행되어 왔다. 예를 들면, Miyazaki 등[7]은 국부 감육의 형상이 탄소강 직관의 파괴거동에 미치는 영향을 실험적 및 해석적으로 검토하였다. Ahn 등[8]은 탄소강 엘보우와 직관 형태의 배관을 대상으로 배관 외부에 감육이 발생한 경우의 파괴모드와 파괴강도에 대해 검토하였다. 그리고 Takahashi 등[9],[10],[11]은 국부 감육을 가지는 탄소강 엘보우와 직관 배관을 대상으로 국부 감육이 배관의 정적 및 저사이클 피로 파괴거동에 미치는 영향을 실험적으로 검토하였다. 이와 같이 배관의 감육에 대한 연구는 주로 탄소강 배관을 대상으로 하고 있으며, 현재 널리 사용되고 있는 스테인리스강 배관의 파괴거동과 파괴강도에 대한 연구가 부족한 실정이다. 그리고 균열이 발생한 배관의 파괴거동 및 파괴강도에 대한 연구도 부족한 실정이다. 따라서 에로젼/코로젼, 이종금속접촉부식, 용접부의 응력부식 및 상시 진동에 의해 우려되는 스테인리스강 배관의 감육과 균열에 대한 안전성 검토가 필요하다[12].
본 연구에서는 실제 원자력 발전소의 배관에 사용되고 있는 직경 3인치 엘보우 및 직관 형태의 스테인리스강(TP316) 배관에 단조하중 및 반복하중 재하실험을 실시하여 국부적으로 발생한 감육과 균열의 정도가 배관의 파괴모드 및 파괴강도에 미치는 영향을 실험적으로 평가하였다. 그리고 ASME[13]Code Section Ⅲ, DivisionⅠ, NB-3656의 설계 휨 모멘트와 실험에서 구한 최대 휨 모멘트를 비교하여 ASME의 결함 허용기준을 평가하였다.
2. 시험체 제작 및 실험방법
2.1 시험체 제작
본 실험에서는 스테인리스강(TP316)을 이용하여 Fig. 1과 같이 직경이 3인치(88.90mm)이고 두께가 11.13mm인 엘보우 시험체와 직관 시험체를 제작하였다.
엘보우 시험체는 길이 170mm 직관 2개에 90° 곡관을 맞대기 용접하여 제작하였으며, 리듀서를 가지는 직관 시험체는 길이 100mm 리듀서에 200mm 직관을 맞대기 용접하여 제작하였다. 응력부식균열, 용접부의 초기결함 또는 상시진동에 의해 우려되는 균열은 Fig. 1의 용접부 A-A단면에서 발생할 것으로 예상된다. 그리고 실제 배관에서의 유속에 의한 국부적인 감육은 Fig. 1의 B-B단면과 같은 위치에서 발생할 것으로 예상된다. 이에 본 연구에서는 Fig. 2와 같이 감육과
(a) Elbow Pipe Specimen
(b) Straight Pipe Specimen
Fig. 1 Geometry of Specimens (unit; mm)
균열을 인위적으로 도입하였다. 배관의 직경이 3인치로 작기 때문에 용접 후에 전기방사장비, 전동공구 등을 사용하여 결함을 모사하기 어려우므로 맞대기 용접접합 전에 결함을 도입하였다.
균열은 관의 중심을 기준으로 60° 만큼의 원호 길이로 편면 부분 개선하고 나머지 부분은 편면 V개선하여 용접하였다. 즉 부분 개선된 영역에서는 용입부족으로 초기 균열이 도입되고 나머지 부분은 완전 맞대기 용접이 되도록 하여, Fig. 2(a)와 같이 초기 관두께의 0%, 35%, 75% 균열을 도입하였다. 그리고 국부적인 감육은 엔시공작기계를 이용하여 시험체의 종방향으로 길이 100mm, 관의 중심을 기준으로 60° 만큼의 원호 길이로 기계 가공하여 이들 영역의 두께를 Fig. 2(b)에서 나타낸 것과 같이 초기 관두께의 0%, 35%, 75%로 감육하였다. 이와 같이 균열 및 감육을 도입한 후 맞대기 용접하고, 배관의 양단부는 동일 재질의 스테인리스(TP316) 원형강판을 용접하여 배관내부가 완전 밀폐되도록 하였다. 각 시험체의 내부에 20MPa의 수압을 가하기 위한 입구 및 출구 노즐을 2개씩 설치하였고, 하중 재하를 위한 첨접강판도 부착하였다.
본 실험에서 사용한 시험체의 형상, 결함의 종류 및 정도를 Table 1에 나타내었다. 배관의 형상은 엘보우와 직관 2가지이고, 사용개수는 각각 10개로 총 20개를 대상으로 하였으며 이 중에서 5개씩은 단조하중 재하실험에, 나머지 5개씩은 반복하중 재하실험에 사용하였다. 사용된 스테인리스강(TP316)의 인장강도는 515MPa, 항복강도는 205MPa, 탄성계수는 200GPa, 연신율은 40%이다. TP316의 화학구성성분은 Table 2에 나타내었고, 용접조건은 Table 3에 나타내었다.
(a) Local Initial Crack
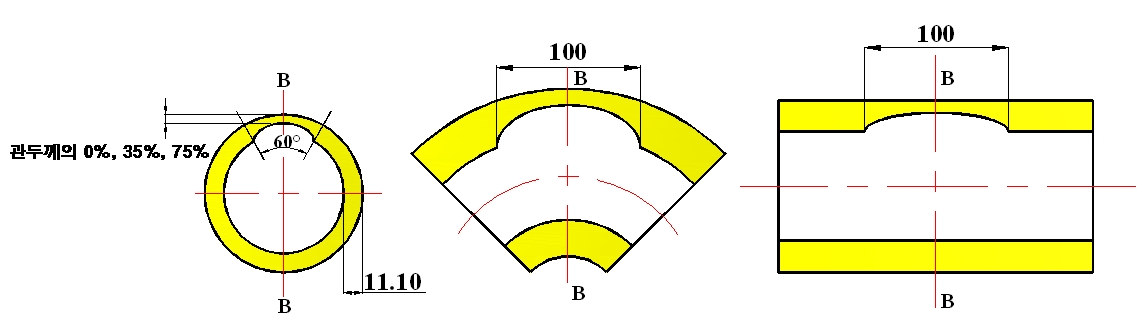
(b) Local Wall Thinning
Fig. 2 Detail of Initial Crack and Wall Thinning (unit; mm)
Specimen Type |
Specimen name |
Defect ratio (a/t) |
Initial Crack (degree) |
Wall Thinning (degree) |
Notation |
Elbow pipe (monotonic and repeated load) |
EL_REF |
0 |
0 |
0 |
시편명 표기 예) EL_C75: ELbow 시편, Crack 75%인 시험체 |
EL_C35 |
0.35 |
60 |
0 |
||
EL_C75 |
0.75 |
||||
EL_W35 |
0.35 |
0 |
60 |
||
EL_W75 |
0.75 |
||||
Straight pipe (monotonic and repeated load) |
CA_REF |
0 |
0 |
0 |
CA_W75: CAntilever 시편, Wall thinning 75%인 시험체 |
CA_C35 |
0.35 |
60 |
0 |
||
CA_C75 |
0.75 |
||||
CA_W35 |
0.35 |
0 |
60 |
||
CA_W75 |
0.75 |
C |
Si |
Mn |
P |
S |
Ni |
Cr |
Mo |
≦ 0.08 |
≦ 1.00 |
≦ 2.00 |
≦0.04 |
≦0.03 |
12.00 |
16.00 |
2.00 |
용접법 |
용접봉의 품명 |
용접 전압 (Volt) |
용접 전류 (Amp) |
용접 속도 (cm/min) |
입열량 (kJ/cm2) |
GTAW |
AWS A5.9 ER316L, 2.4pi, DCEN |
8-15 |
90-180 |
5-20 |
5.7-17.8 |
(a) Test Setup (a) Test Setup
(b) Loading System (b) Loading System Fig. 3 Elbow Pipe Specimen Fig. 4 Straight Pipe Specimen |
2.2 실험방법
본 실험에서의 엘보우 시험체와 직관 시험체의 실험 전경 및 하중재하를 Fig. 3과 4에 나타내었다. 하중은 1,000kN의 동적 UTM을 이용하여 단조하중과 반복하중을 재하 하였다.
단조하중 재하실험에서는 Fig. 3에 나타낸 것과 같이 엘보우 시험체의 경우 압축하중을 가하여 감육과 균열이 있는 외호면(extrados)에서 인장응력이 발생하도록 하중을 재하 하였다. 그리고 리듀서를 가지는 직관 시험체에서도 Fig. 4에 나타낸 것과 같이 감육과 균열이 있는 부분에서 인장응력이 발생하도록 하중을 재하 하였다.
(a) Intrados
(b) Extrados
Fig. 5 Ovalization of Elbow Pipe Specimen
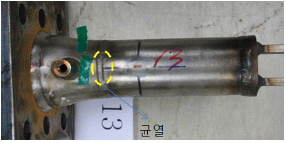
(a) Cracking from Initial Crack
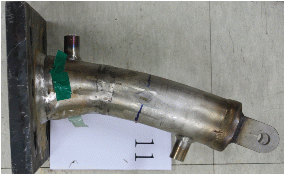
(b) Plastic Deformation
Fig. 6 Typical Failure of Straight Pipe Specimen
하중재하는 변위제어(5mm/min)로 하였으며, 파괴에 의한 누설이 발생하거나 엘보우와 직관 시험체의 수직변위가 각각 150mm 또는 100mm에 도달한 경우에 실험을 종료하였다.
반복하중 재하실험은 단조하중 재하실험의 결과로부터 각 기준시편(결함이 없는 시편)에서 측정된 최대하중의 ± 90%에 해당하는 하중이 발생되는 변위구간(약 ± 20mm)에 대해서 인장과 압축 하중을 반복재하 하였으며, 시험체가 파괴되어 누설이 발생하거나 반복횟수가 180회를 초과하는 경우에 실험을 종료 하였다. 반복하중은 정현파형으로 0.67cycle/ min의 속도로 하였다. 시험체 내부는 실제 배관의 설계 수압과 동일한 20MPa의 내압을 가하였으며, 작용하중과 변위는 UTM의 피드백된 값을 계측하였다.
3. 실험결과 및 분석
3.1 단조하중
3.1.1 파괴모드
엘보우 시험체의 경우에는 파괴되거나 수직변위가 150mm에 도달할 때까지 단조하중을 재하하였다. 그 결과 0%, 35%, 75%의 감육과 균열이 도입된 엘보우 시험체는 Fig. 5에 나타낸 것과 같이 단조하중 재하시 엘보우 시험체에서 발생하는 대표적인 파괴거동 중 하나인 곡관부의 편평화가 발생하였다[3].
직관 시험체의 경우에는 파손이 발생하거나 수직변위가 100mm에 도달할 때까지 단조하중을 재하하였다. 그 결과, 35%와 75%의 균열을 도입한 직관 시험체는 Fig. 6(a)에 나타낸 것과 같이 맞대기 용접부의 초기균열로부터 균열이 진전하여 파괴되었다. 이 이외의 0%, 35%, 75%의 감육과 균열 시편에는 Fig.6(b)에 나타낸 것과 같이 소성변형은 발생하였으나, 균열 및 누수는 발생하지 않았다. 따라서 단조하중을 받는 직관 시험체에 35%, 75%의 균열이 발생한 경우에는 용접부가 직관 시험체의 취약부임을 알 수 있다.
3.1.2 최대하중
단조하중을 재하한 엘보우와 직관 시험체의 하중-수직변위 곡선을 각각 Fig. 7과 8에 나타내었다. 결함이 없는 기준시험체의 최대하중에 대한 감육 및 균열이 도입된 시험체의 최대하중과 기준시험체의 최대하중 차에 대한 비와 파괴모드를 Table 5에 정리하였다.
먼저 엘보우(EL) 시험체의 경우, 35%, 75%의 감육을 도입한 시험체의 최대하중은 0.9%, 6.8% 감소하였다. 용접부에 35%, 75%의 초기균열을 도입한 경우에는 최대하중 비율이 0.2%, 2.4% 증가하는 것으로 나타났으나, 이와 같은 최대하중의 증가는 실험 오차에 기인된 것으로 추정된다. 따라서 단조하중을 받는 엘보우 시험체는 35%, 75%의 균열이 발생하는 경우에도 최대하중의 감소는 거의 발생하지 않음을 알 수 있다. 그러나 75% 감육이 발생한 경우에는 최대하중이 약 7%정도 감소함을 알 수 있다.
직관(CA) 시험체의 경우, 용접부에 35%, 75%의 초기균열이 도입된 시험체의 최대하중은 기준 시험체와 비교하여 각각 9.7%, 17.0% 감소하였다. 그리고 35%, 75%의 감육에 의해서는 최대하중이 0.3% 증가, 3.7% 감소한다는 실험값이 얻어졌지만, 이와 같은 35% 감육에 의한 최대하중의 증가는 실험 오차에 기인하는 것으로 추정된다. 따라서 단조하중을 받는 직관 시험체의 최대하중은 균열이 35%, 75%로 증가함에 따라 9.7%, 17%로 감소량이 증가하고, 35%의 감육에 의한 최대하중의 뚜렷한 감소는 발생하지 않음을 알 수 있다.
Fig. 7 Load-Vertical Displacement Curve of Elbow Pipe Specimen
Fig. 8 Load-Vertical Displacement Curve of Straight Pipe Specimen
3.2 반복하중
3.2.1 파괴모드
반복하중 재하실험은 앞의 단조하중 재하실험으로부터 얻어
진 기준 시험체(EL_REF, CA_REF)의 최대하중이 90%에 해당하는 변위범위(± 20mm)구간으로, 파손이 발생하거나
Specimen |
Maximum load(kN) |
Reduction ratio of maximum load(%) |
Failure mode |
||
EL_REF |
93.21 |
|
0.0 |
|
OV-NF |
EL_C35 |
93.41 |
|
0.2 |
|
OV-NF |
EL_C75 |
95.42 |
|
2.4 |
|
OV-NF |
EL_W35 |
92.39 |
|
-0.9 |
|
OV-NF |
EL_W75 |
86.88 |
|
-6.8 |
|
OV-NF |
CA_REF |
114.12 |
|
0.0 |
|
PD-NF |
CA_C35 |
103.03 |
|
-9.7 |
|
CR-IC |
CA_C75 |
94.70 |
|
-17.0 |
|
CR-IC |
CA_W35 |
114.47 |
|
0.3 |
|
PD-NF |
CA_W75 |
109.86 |
|
-3.7 |
|
PD-NF |
OV-NF: Ovalization-No failure, PD-NF: Plastic deformation-No failure, CR-IC: Cracking from initial crack. |
(a) Intrados
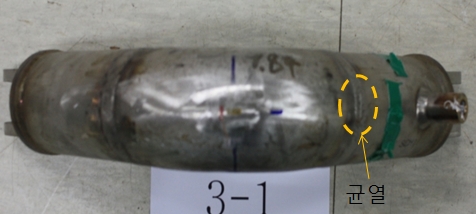
(b) Extrados
Fig. 9 Failure of Elbow Pipe Specimens
(a) Cracking from Weld Toe
(b) Cracking from Initial Crack
Fig. 10 Failure of Straight Pipe Specimens
반복회수가 180회에 도달할 때까지 진행하였다.
엘보우 시험체의 파괴양상은 Fig. 9(a)에 나타낸 것과 같이 내호면에서 균열이 발생하여 파괴되거나, Fig. 9(b)에 나타낸 것과 같이 곡관부와 직관부의 맞대기 용접부에 도입된 균열에서의 균열 진전으로 인해 파괴되었다. 기준 시험체(EL_ REF)와 35%의 균열이 도입 된 시험체(EL_C35)는 반복회수 180회까지 균열 및 파손이 발생하지 않았으나, 75%의 균열이 도입 된 시험체(EL_C75)는 용접부에 도입된 초기균열의 진전으로 반복회수 13회에 파괴가 발생하였다. 그리고 35%, 75% 감육 시험체(EL_W35, EL_W75)는 각각 반복회수 112회와 117회에 내호면에서 균열 및 누수가 발생하였다. 따라서 반복하중을 받는 엘보우 시험체에 35%, 75%의 감육과 균열이 발생한 경우에는 균열이 도입 된 용접부가 엘보우 시험체의 취약부임을 알 수 있다.
(a) EL_REF ![]() (b) CA_REF
(c) EL_C75 ![]() (d) CA_C75 Fig. 11 Load-Vertical Displacement Curve Under Repeated Load |
3.2.2 변형에너지 흡수율
엘보우와 직관의 기준 시험체와 75% 균열이 도입 된 시험체의 하중-변위 곡선을 Fig. 11에 나타내었다. 이 하중-변위곡선은 반복하중 재하실험에서 시험체와 UTM을 연결하는 핀 연결부의 유격, 즉 핀의 직경에 비하여 첨접판 구멍 직경이 커서 하중은 작용하지 않지만 변위가 증감하는 구간이 발생하였다. 그러나 엘보우와 직관 시험체에서 각각 동일한 핀 연결부의 유격을 가지고 있어, 변형에너지의 상대적인 비교는 가능하다. 먼저 하중-변위 이력곡선의 내부면적으로 변형에너지를 계산하고 기준 시험체의 변형에너지에 대한 각 시험체의 변형에너지와 기준 시험체의 변형에너지의 차의 비로 변형에너지 흡수율을 계산하였다. 각 시험체의 변형에너지 흡수율과 파괴모드를 Table 6에 나타내었다.
엘보우 시험체의 경우, 기준 시험체(EL_REF)의 에너지 흡수량과 비교하여 35%, 75% 균열이 도입 된 시험체(EL_C35, EL_C75)는 각각 16%, 94% 감소하였다. 35%, 75% 감육이 도입된 시험체(EL_W35, EL_W75)는 각각 46%, 51% 감소하였다. 그러나 이는 기준 시험체의 반복재하 시험을 180회에 종료하였고, 35% 균열 시험체 또한 180회에 시험을 종료하여 이를 기준으로 계산한 값이므로, 180회 이상 시험을 계속하였다면 35% 균열 시험체를 포함한 나머지 시험체의 에너지 흡수율은 더욱 더 감소할 것이다.
Specimen |
Displacement Amplitude [mm] |
Force Amplitude [kN] |
Strain Energy[kN/mm] |
Strain Energy ratio(%) |
Cycle |
Failure mode |
|
EL_REF |
40.6 |
220.8 |
3.49E+05 |
0 |
|
180 |
PD-NF |
EL_C35 |
40.3 |
225.8 |
2.94E+05 |
-16 |
|
180 |
PD-NF |
EL_C75 |
40.2 |
184.3 |
2.01E+04 |
-94 |
|
13 |
CR-IC |
EL_W35 |
40.2 |
197.7 |
1.88E+05 |
-46 |
|
112 |
CR-IN |
EL_W75 |
40.5 |
174.3 |
1.71E+05 |
-51 |
|
117 |
CR-IN |
CA_REF |
40.2 |
237.2 |
2.92E+05 |
0 |
|
141 |
CR-WT |
CA_C35 |
40.2 |
238.9 |
1.82E+04 |
-94 |
|
4 |
CR-IC |
CA_C75 |
40.2 |
195.7 |
2.45E+03 |
-99 |
|
1 |
CR-IC |
CA_W35 |
40.5 |
244.3 |
4.23E+05 |
45 |
|
180 |
PD-NF |
CA_W75 |
40.2 |
238.8 |
2.90E+05 |
-1 |
|
180 |
PD-NF |
PD-NF: Plastic deformation-No failure, CR-IC : Cracking from initial crack, CR-IN : Cracking at intrados, CR-WT: Cracking at weld toe |
4. ASME 기준과의 휨 모멘트 비교
ASME[13]는 원자력발전소 배관의 설계방법을 ASME CODE Section Ⅲ, DivisionⅠ, Subsection NB, NC, ND에 규정하고 있다. 그리고 ASME 기준을 기초로 한 평가 모듈로서 ASME CODE Sec.Ⅺ, DivisionⅠ에서는 가동중 결함이 발생한 배관에 대한 평가 절차 및 교체, 보수, 계속사용에 대한 판단 지침을 제공하고 있다.
본 실험에 사용 된 시험체는 ASME CLASS 1 SA-312 GRADE TP316배관이기 때문에 ASME CODE Section Ⅲ, DivisionⅠ, Subsection NB 항목에 해당된다. 본 절에서는 실험결과를 이용하여 ASME 기준에 의한 원자력발전소 배관에 사용되는 최소 관 두께 기준의 만족여부와 설계 휨 모멘트를 평가한다.
4.1 최소 두께 기준
원자력발전소 배관에 사용되는 최소 배관 두께(tmin)는 ASME CODE Section Ⅲ, DivisionⅠ, NB-3640에 제시되어 있는 식 (1)을 이용하여 계산할 수 있다. 그리고 계산된 배관 두께의 최대 허용 내압은 식 (2)로 계산할 수 있다.
(1)
(2)
Defect ratio/ thickness [mm] |
Minimum required wall thickness [mm] |
Test internal pressure [MPa] |
Maximum allowable internal pressure [MPa] |
|
0% |
11.13 |
6.09 |
20 |
38.40 |
35% |
7.24 |
24.02 |
||
75% |
2.78 |
8.86 |
여기서, P=배관내부의 작용 압력(MPa), Do=외경(mm), t=배관두께(mm), Sm=배관허용응력(MPa), y=0.4, A= 0.0(결함을 고려한 여유 두께)이다.
본 실험에서와 같이, 20MPa의 내압이 작용하는 경우의 최소 배관두께는 식 (1)을 이용하고, 배관에 결함이 발생한 경우에는 결함으로 인해 감소 된 배관 두께를 식 (2)에 대입하여 결함이 있는 경우의 최대 허용 내압을 구할 수 있다. 20MPa의 내압이 작용하고, 0%, 35%, 75%의 감육과 균열이 발생한 경우 계산된 최소 배관 두께 및 최대 허용 내압을 Table 7에 나타내었다. 먼저 내압 20MPa이 작용하는 경우의 최소 배관두께는 6.09mm로 75%의 감육과 결함이 도입한 시험체는 ASME 기준을 만족하지 않는다. 그리고 75% 감육과 균열이 발생한 경우의 최대 허용내압은 8.86MPa로 본 실험의 20MPa보다 작으므로 ASME 기준을 만족하지 않는다. 따라서 0%와 35% 감육과 균열 시험체는 ASME 기준을 만족하지만, 75% 감육과 균열 시험체는 ASME 기준을 만족하지 않는다.
4.2 단조하중 재하시 최대 휨 모멘트 비교
ASME CODE Section Ⅲ, DivisionⅠ, NB-3640에 제시 된 식 (3)을 이용하여 단조하중 작용하의 설계 휨 모멘트를 계산할 수 있다.
(3)
여기서 B1, B2는 ASME CODE Section.Ⅲ Table NB-3681(a)-1과 NB-3683.7에 의한 직관과 엘보우 시험체의 주응력지수로 Table 8과 같다.
ASME의 식 (3)을 이용하여 아무런 결함이 도입 되지 않은 기준 시험체에 대해 계산한 설계 휨 모멘트와 실험으로 구한 각 시험체의 최대 휨 모멘트를 Table 9에 나타내었다. 최대 휨모멘트는 변위제어에 의한 단조하중 재하시 동적 UTM의 로드셀에 의해 피드백 된 하중값의 최대값과 이때의 수평변위를 곱하여 계산하였다. 그리고 휨 모멘트비는 ASME의 설계 휨
주응력 지수 |
직관시편 |
엘보우 시편 |
Condition |
B1 |
B1=0.5 |
B1=-0.1+0.4h |
but not <0 nor >0.5 |
B2 |
B2=1.0 |
B2=1.3/h2/3 h=t×R/rm2 rm=(DO-t)/2 |
but not<1.0 |
Specimen name |
ASME 설계 휨 모멘트 [KN·mm] |
실험에 의한 최대 휨 모멘트 [KN·mm] |
휨 모멘트 비 |
EL_REF |
10,860 |
26,521 |
2.44 |
EL_C35 |
26,744 |
2.46 |
|
EL_C75 |
27,708 |
2.55 |
|
EL_W35 |
26,747 |
2.46 |
|
EL_W75 |
25,304 |
2.33 |
|
CA_REF |
17,675 |
24,322 |
1.38 |
CA_C35 |
21,338 |
1.21 |
|
CA_C75 |
18,882 |
1.07 |
|
CA_W35 |
24,013 |
1.36 |
|
CA_W75 |
22,762 |
1.29 |
모멘트에 대한 실험에 의한 최대 휨 모멘트의 비로 나타내었다.
엘보우 시험체의 휨 모멘트비는 결함이 없는 기준 시험체에서 2.44이고, 35%, 75%의 감육과 균열이 발생한 경우에도 2.33∼2.55였다. 따라서 감육과 균열의 결함종류와 0%, 35%, 75%의 결함정도에 상관없이 엘보우 시험체의 휨 모멘트는 거의 동일하고, 35%, 75%의 감육과 균열 발생에 의한 엘보우 시험체의 휨 모멘트 감소는 미미함을 알 수 있다. 그리고 엘보우 시험체의 휨 모멘트는 35%, 75%의 감육과 균열이 발생한 경우에도 ASME 설계 휨 모멘트의 2.33배 이상임을 알 수 있다.
직관 시험체의 휨 모멘트비는 결함이 없는 기준 시험체에서 1.38이고 균열과 감육이 35%에서 75%로 증가함에 따라 모멘트비는 각각 1.21에서 1.07, 1.36에서 1.29로 감소하였다. 따라서 직관 시험체의 휨 모멘트비는 감육과 균열의 결함 정도가 증가할수록 감소하지만, 35%, 75%의 감육과 균열이 발생한 경우에도 ASME 설계 휨 모멘트 이상임을 알 수 있다.
5. 결 론
본 연구에서는 0%, 35±5%(이하 35%로 표기), 75±5%(이하 75%로 표기)의 감육과 균열을 도입한 직경 3인치 스테인리스강 엘보우와 직관 시험체의 단조하중 및 반복하중 재하실험을 실시하여 국부 감육과 균열이 스테인리스강 배관의 파괴거동에 미치는 영향을 평가하였다. 주요한 결과를 정리하면 다음과 같다.
(1) 단조하중을 받는 엘보우 시험체는 감육과 균열의 결함종류 및 0%, 35%, 75%의 결함정도에 상관없이 동일하게 편평화가 발생하였지만, 균열 및 누수는 발생하지 않았다. 그리고 직관 시험체는 35%, 75%의 초기균열이 도입된 경우에만 용접부에서의 균열진전으로 인한 파괴가 발생하였다.
(2) 단조하중을 받는 엘보우 시험체의 최대하중은 결함이 없는 기준 시험체와 비교하여 35%의 감육, 35%와 75%의 균열이 도입된 시험체는 거의 동일하고 75% 감육이 된 경우에 약 7%정도 감소하였다. 그리고 직관 시험체의 경우에는 35%, 75%의 감육에 의한 최대하중의 감소는 발생하지 않았으며, 35%, 75%의 균열에 의해 각각 약 10%, 17% 감소하였다.
(3) 반복하중을 받는 엘보우와 직관 시험체는 곡관부의 내호면, 균열도입부 또는 용접토우에서의 균열 발생 및 진전에 의한 파괴가 발생하였다.
(4) 반복하중이 작용하는 경우 엘보우 시험체의 변형에너지는 결함이 없는 기준 시험체에 비해 75%의 균열과 35%, 75%의 감육에 의해 각각 94%, 46%, 51% 이상 감소하였다. 직관 시험체의 경우에는 35%, 75%의 균열에 의해 각각 94%, 99% 감소하였다.
(5) 엘보우 시험체의 최대 휨 모멘트는 35%, 75%의 감육과 균열 발생에 상관없이, 결함이 없는 기준 시험체와 거의 동일하였다. 직관 시험체의 최대 휨 모멘트는 0%, 35%, 75%로 감육 및 균열 정도가 증가함에 따라 감소하였다.
(6) 35%, 75%의 감육과 균열이 도입된 엘보우와 직관 시험체의 최대 휨 모멘트는 각각 ASME 설계 휨 모멘트의 2.3배와 1.07배 이상이었다.
Acknowledgments
본 연구는 2011년 원자력연구개발사업의 일환으로 교육과학기술부, 원자력연구원의 지원을 받아 수행되었습니다(2011- 0001901).
References
- 김문수, 김상윤, 이성규, 최오선, 현창헌(2008) 극한하중에 대한 원전구조물의 설계기준 고찰, KINS/RR-578, 한국원자력안전기술원.Kim, M.S., Kim, S.Y., Lee, S.K., Choi, H.S., and Hyun, C.H. (2008) Investigation of design code of nuclear plant facilities under extreme loads, KINS/RR-578, Korea Institute of Nuclear Safety (in Korean).
- 안석환, 남기우, 김선진, 김현수, 김진환, 도재윤(2001) 감육배관의 파괴거동 평가, 대한기계학회 2001년도 추계학술대회논문집 A, 대한기계학회, pp.61-66.Ahn, S.H., Nam, K.W., Kim, S.J., Kim, H.S., Kim, J.H., and Do, J.Y. (2001) Fracture behavior evaluation of pipes with local wall thinning, Proceeding of KSME 2001 Fall Annual Meeting, KSME, pp.61-66 (in Korean).
- 안석환, 남기우(2006) 감육된 탄소강배관의 변형과 파괴거동, 한국해양공학회지, 한국해양공학회, 제20권, 제4호, pp.17-23.Ahn, S.H. and Nam, K.W. (2006) Deformation and fracture behavior of wall thinned carbon steel pipes, Journal of Ocean Engineering and Technology, KSOE, Vol. 20, No. 4, pp.17-23 (in Korean).
- 김인태, Kainuma, S., 정진환(2008) 콘크리트에 접해있는 강재의 국부부식과 피로손상, 한국강구조학회 논문집, 한국강구조학회, 제20권, 제2호, pp.313-321.Kim, I.T., Kainuma, S., and Cheung, J.H. (2008) Local corrosion and fatigue damages of steel plates at the boundary with concrete, Journal of Korean Society of Steel Construction, Vol. 20, No. 2, pp.313-321 (in Korean).
- 김인태, 장홍주, 정지영(2010) 가시설 부식 강재의 잔존 인장 내하성능 평가에 관한 실험적 연구, 한국강구조학회 논문집, 한국강구조학회, 제22권, 제5호, pp.399-409.Kim, I.T., Chang, H.J. and Cheung, J.Y. (2010) An experimental study on the evaluation of residual tensile load-carrying capacity of corroded steel plates of temporary structure, Journal of Korean Society of Steel Construction, Vol. 22, No. 5, pp.399-409 (in Korean).
- 박진은, 경갑수, 안용모, 권순철(2011) 실데이터 분석을 통한 지역난방 열배관의 피로안전성 평가, 한국강구조학회 논문집, 한국강구조학회, 제23권, 제5호, pp.569-579.Park, J.E., Kyung, K.S., An, Y.M., and Kwon, S.C. (2011) Fatigue evaluation of district heat pipes based on the measured data, Journal of Korean Society of Steel Construction, Vol. 24, No. 5, pp.569-579 (in Korean).
- Miyazaki, K., Nebu, A., Kanno, S., Ishiwata, M., and Hasegawa, K. (2002) Study on fracture criterion for carbon steel pipes with local wall thinning, Journal of High Pressure Institute of Japan, JHPI, Vol. 40, No. 2, pp.62-72 (in Japanese).
- Ahn, S.H., Nam, K.W., Yoo, Y.S., Ando, K., Ji, S.H., Ishiwata, M., and Hasegawa, K. (2002) Fracture behavior of straight pipe and elbow with local wall thinning, Nuclear engineering and Design, pp.91-103.
- Takahashi, K., Ando, K., Kimura, Y., Kawato, K., Hisatsune, M., and Hasegawa, K. (2004) Failure behavior of pipe having orifice undergoing local wall thinning in downstream region of orifice, Journal of High Pressure Institute of Japan, JHPI, Vol. 42, No. 6, pp.310-317 (in Japanese).
- Takahashi, K., Kato, A., Ando, K., Hisatsune, M., and Hasegawa, K. (2007) Fracture and defor- mation behaviors of tee pipe with local wall thinning, Nuclear engineering and Design, pp.137-142.
- Takahashi, K., Ando, K., Watanabe, S., Hisatsune, M., Hidaka, A., and Miyazaki, K.(2008) Low cycle fatigue behaviors of elbow pipe containing local wall thinning, Journal of High Pressure Institute of Japan, JHPI, Vol. 46, No. 6, pp.352-362 (in Japanese).
- 최영환, 정연기, 김용범, 박윤원, 이정배, Wilkowski, G. (1996) 원주방향 균열을 가진 원전 배관의 하중지지능력에 관한 실험적 연구, 대한기계학회 춘계학술대회논문집, 대한기계학회, pp.31-36.Choi, Y.H., Chung, Y.K., Kim, Y.B., Park, Y.W., Lee, J.B. and Wilkowski, G. (1996) An experi- mental study on the load carrying capacity of nuclear piping with a circumferential crack, Proceeding of KSME 1996 Spring Annual Meeting, KSME, pp.31-36 (in Korean).
- American Society of Mechanical Engineer (2007) ASME Boiler & Pressure Vessel Code Section Ⅺ, ASME, USA.